Willard SaysâŚâŚ
Heeling-off frustrates the hell out of operators. Their quest for vacuum seemly has no end. Swing, raise, lower, swing right, lower, swing leftâŚnothing succeeds for very long. An increase in vacuum raises soon-to-be-dashed expectations as it sags back down to near clear-water value. More maneuvering, more searching, more raising, lowering, swingingâŚ
Such is the lot of an operator trying to produce using a ladder that is afflicted with heeling-off syndrome.
Many owners evidently accept heeling-off, and its accompanimentâlow production, as if that were their fate; nothing can be done; lousy production is our lot in life; maybe someday our luck will change. They persevere: âWe are losing fifty cents a ton but we will make it up by pumping more hours.â
Rejoice! Help is at hand! Read on! The salvation that is high production can be yours!
We get frequent calls seeking solutions to production problems. First, we ask a lot of questions; delve into the guts of their operation; try to pinpoint the exact cause or causes of their problem or problems. Usually, we can get a pretty good picture of what they are doing and the nature of their difficulty. The profit motive always brings delight when we find a producer who will benefit by buying our products or services.
Conversely, we also find satisfaction in helping a producer prosper by following our advice; advice unavailable from any other source.
Case history:
A dredge owner called to inquire as to whether or not a different basket for his rotary cutter might cure his low production problem. He had pictures of our sand and gravel baskets and wanted to know more about them; thought one of them might work better than his bladed basket.
Several questions later, the cause of his problem became apparent:
- The cutter very seldom stalls.
- There is very little oversized rock in the deposit.
- There are layers of clay in the deposit-probably no more than 6 inches thick.
- The basket never plugs with clay or rocks.
- Cannot maintain the desired vacuum.
- Vacuum rises after moving the cutter and then tapers off.
- Maneuvering the cutter is difficult at times especially at shallow depths.
- Cannot dig down to increase vacuum.
- Often cannot swing sideways to increase vacuum without raising the ladder.
- Fifty-foot-long straight ladder.
- Digging depth of only 15 to 20 feet at times.
The ladder on the dredge in question was about as straight as it could be. The bottom of the cutter basket protruded only a few inches below the bottom of the frame/suction pipe.
A clear-cut case of heeling-off. A clear violation of Dredge Commandment VI, which dictates that pumpable solids be continually available at the suction inlet.
The Solution
Install a âDutchman.â A Dutchman? No, you wonât have to recruit an operator from Holland. Wonât cost much money. A little cuttinâ and weldinâ will do. A Dutchman is a downward bend in the suction pipe/ladder frame near the digger end of the rotary cutter ladder. This modification makes it possible for the rotary cutter/suction inlet to stay in contact with the solids bank even at very shallow digging depths.
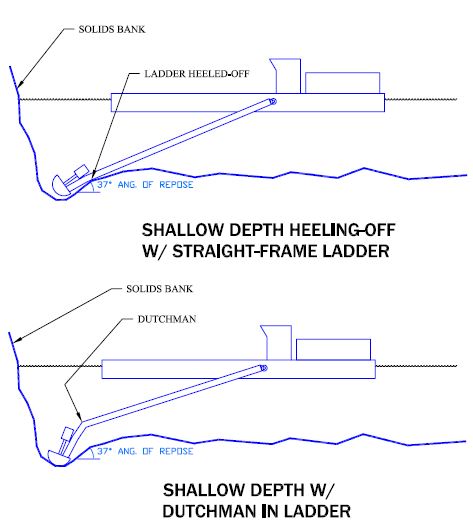
Angle of Repose
An aggregate stockpile is commonly considered to have an angle of repose of about 37 degrees above horizontal. That means from level ground a bulldozer would have to tip up at an angle of 37 degrees to crawl up the stockpile assuming that it could get sufficient traction.
The underwater angle of repose of loosened solidsâthat material that has sloughed off of the in situ (undisturbed) bank of solidsâis about the same as a dry stockpile. The in situ angle of repose depends on the nature of the deposit. Some banks stand nearly vertical while others cave-in very easily to form an angle of repose of 25 degrees or less.
If the loosened solids do repose at an angle of about 37 degrees, a dredge with a straight, 50- foot-long ladder will have to mine at a depth of at least 30 feet to achieve a ladder-down angle of 37 degrees. At depths of less than 30 feet the bottom of the ladder/suction pipe will come to rest on the bank of loosened solids and the digger/suction inlet will not be able to penetrate any further into the deposit. The digger/suction inlet, unable to be kept in contact with the solids bank, âpulls inâ at a steadily diminishing rate, all the solids the inrushing water can entrain. Soon, a clear-water vacuum reading will reflect the fact that only clear water is entering the suction inlet.
Attempts to swing sideways when the ladder is resting on the solids bank are very difficult because the ladder/suction pipe must bulldoze material out of the way as it moves. Production suffers while the operator strives to maneuver the digger into the solids bank and increase vacuum.
How do dredgers get into such a pickle?
They:
- Buy a dredge with a ladder that is too long.
- Buy a cumbersome, direct-diesel-drive ladderpump dredge with 45-degree maximum tilt.
- Find that the âfloorâ of their pit rises to cause diminished digging depth.
- Buy a dredge with a digger that is incapable of mining to the full depth of the deposit (rotary cutter vis-Ă -vis linear cutter).
If your situation fits the first, second or third of these scenarios, a Dutchman will likely solve your problem. If you are a victim of unrealized production because you bought a rotary cutter for an application where only a linear cutter will do, a Dutchman will not help much.
The fourth scenario often goes like this. Drill logs show that the good material in the deposit extends to 60 feet below water; rotary cutter mining will not go deeper than about 40 feet; the cutter runs into a lot of oversize or âhardpan;â cutter breakage is common and production is poor. Installing a Dutchman may help, but only for a while. The presence of oversize will soon frustrate the digging action of a rotary cutter; the oversize rocks act like ball bearings to keep the basket from penetrating deeper into the deposit.
Install a linear cutter and put the quietus to fourth scenario problems. Call us, we are linear cutter experts.
The Dutchman
We advised the Case History caller to install a Dutchman in his ladder by canting an eight-foot- long end section of the frame, including the cutterhead assembly and suction pipe, downward about 35 degrees. This modification will permit the digger/suction inlet to remain immersed in pumpable solids at any digging depth. Solids can then slide downward toward the suction inlet from all directions to maintain production because the ladder frame/suction pipe will no longer come in contact with the solids bank. The digger can be crowded right, left or downward to assure continuous production.
Success
These folks made the modification over the next two days and immediately average production more than doubled. Soon they had stockpiles; saleable aggregate in ample supply; production in excess of demand; a delightful change of circumstance; no more numbing, long hours pursuing paltry production.
If you are
suffering from the heartbreak of heeling-off, go to the Dutchman store and get
your own.
Linear Cutter? Heeling-Off?
It seems likely that since a linear cutter is a trench-cutting device, it is immune to the problem of heeling-off. Au contraire; tainât so. Linear cutters suffer from this syndrome with the same consequences that accrue to rotary cutters. The problem is not as acute with linear cutters because simply allowing the ladder to dig down into the deposit always results in some production. For that reason, linear cutter owners may be suffering reduced production due to a little heeling-off and not realize it.
The proof of the pudding is in the eating; the proof of linear cutter heeling-off is a slack hoist rigging coupled with low vacuum. The suction inlet cannot stay immersed in pumpable solids because it is being held up while the chain excavates material from under the ladder as fast as it can.
The rate of production depends on:
- How much chain is in contact with in situ solids.
- The chain speed.
- The chainâs digging capability.
- The length of the âcut.â
Ideally, only about five feet of chain should be in contact with in situ solids. The goal is always to keep the suction inlet immersed in pumpable solids. If the chain cannot dig downward fast enough to satisfy that goal, production will be less than it could be. The ladder may be too long, but the more frequent cause of linear cutter heeling-off is advances that are too long. At the completion of each swing across the cutting arc, the dredge should be advanced only about five feet. Longer advances usually prevent the suction inlet from staying immersed in excess pumpable solids (heeling-off) with a consequent reduction in production. If a linear cutter ladder is so long that the maximum angle of incline is less than about 25 degrees, it should be shortened.
We have built linear cutters with removable ladder frame and pontoon sections so that the overall dredge length can be altered to suit the digging depth.
It is not an impossible task to shorten a full-length linear cutter. Whatever the cost, improved production will make the effort very worthwhile.
Repeatedly, reference has been made to keeping the suction inlet immersed in pumpable solids. That could provoke the question, âWonât that cause cavitation or choke-off?â Yes it could, but it wonât if the dredge has a CONVAC modulating bypass valve. CONVAC assures full, uninterrupted production as long as the suction inlet is immersed in pumpable solids. Better check out that CONVAC thingy.
Comment, question, criticism, information on products mentioned? Contact