Willard SaysâŚâŚ
Suction jet assist makes the equivalent of an extra 10 or 15 inches of effective vacuum available at the dredge pump inlet. Effective vacuum is the total amount of vacuum that can be utilized to raise solids up to the pump inlet port. More is better.
Consider for example, a dredge that is maintaining 20 to 22 inches of vacuum without a jet while producing solids at the rate of 250 tph from a depth of 35 feet. Add a jet system to that dredge and it will be able to maintain the same 250 tph from 35 feet with an operating vacuum of perhaps only 9 inches.
The increase in effective vacuum gives the operator some options. He could increase the operating vacuum to 20 to 22 inches and increase solids production to 350 tph from a depth of 35 feet. Or, he could go deeper, perhaps to 55 or 60 feet, and still maintain a production rate of 250 tph.
Jet Assist Facts:
- Primes the dredge pump automatically. Numerous times I have heard operators tout pump priming as the jetâs greatest benefit. If that is all it does, it is a damned expensive priming system.
- Diminishes the effects of cave-ins. The jet system provides from 30 to 50 percent of the water flowing through the dredge system. Small cave-ins will have less effect on dredge operation because a significant proportion of the water required by the pump comes in through the jet and less water has to come in through the suction inlet. Without a jet, a small cave-in will likely require that the suction be raised to reduce vacuum and assure the full flow of liquid to the pump.
- Does not guarantee against discharge pipeline plugging. If a cave-in seals off the suction inlet, the dredge pump will receive only 30 to 50 percent of the total flow that is required to maintain system velocity. That condition will cause the pump to cavitate, the velocity to fall and solids to fall out of the flow until the suction is cleared.
- Does not make more solids available at the suction inlet. To the contrary, the installation of a jet system can actually decrease the dynamic action of water near the suction inlet. A significant portion of the water flowing through the dredge system is injected by the jet, which causes a corresponding reduction in the amount of water entering the suction inlet. Lower flow means that pumpable solids have to be readily available closer to the suction inlet.
- Causes low suction inlet velocity unless proper precautions are taken. The section of suction pipe between the suction inlet and the inlet of the jet assist body should be one pipe size smaller than the pipe connected to the jet discharge port. Using a one-size-smaller pipe will restore some of the velocity reduction caused by the injection of water through the jet.
- Does not add energy to the discharge side of the dredge pump. An unintended consequence occurs when the jet enables an increase in the rate of production. The consequence of higher production is that more pump speed and power will be required to move the additional solids from the pump to the discharge point. Power and speed that may not be available.
- Low efficiency is a fact of life when considering a suction jet assist. A water pump can achieve an efficiency of about 90 percent and a dredge pump about 65 percent. The best manufactured jet assist is less than 20 percent efficient. Homemade jets are likely to be even less efficient.
- 110 psi water pressure is required to obtain good jet performance.
- 30 to 50 percent of the water flowing in the dredge system must be injected through the jet.
- Horsepower required to drive the jet system water pump must equal 33 to 50 percent of the horsepower devoted to driving the dredge pump.
- A dedicated power unit is required to run the jet water supply pump. Jet water flow and pressure requirements must be maintained under all dredge-operating conditions. Dredge pump power unit speed should vary to suit dredge system conditions.
- No jets in the discharge pipeline! In fact, it will have a negative effect on the performance of dredge pipeline system. Consider a pipeline that is flowing at 14 fps before entering the jet body. If the jet adds 50 percent more water to the system, the velocity leaving the jet must increase to 21 fps. The increased friction caused by the higher velocity cannot be overcome by the energy added by the inefficient jet to say nothing of adding extra energy to accomplish the overall effort to move solids to the discharge point.
- Cost efficiency can be realized if the jet is used to solve certain problems. It should be installed only after every effort has been made to achieve maximum production from the dredge. All improvements made to a dredge will be of benefit if, and when, a jet assist system is installed.
Production-Limiting Problems
The productive capacity of a dredge can be reduced by some of the common problems listed below. Eliminate these problems and hopefully, increase production without need for a jet.
You may conclude that I am anti-jet because I spend so much time explaining what a jet will not do. That is precisely the point. I see many dredges that could produce at much higher rates if some improvements were installed. Hopefully, some owners will benefit and find that they can achieve satisfactory production without having to install a jet. All of these papers are offered to help owners save money, reduce cost and increase profit. Installing an unneeded jet is a leap in the wrong direction. Often, under the right conditions, installing a jet is the right move. It is important to make the right decision.
Note; Aside from the cost of correcting the problems listed below, none of the solutions result in increased operating costs. Instituting these improvements will result in increased production and reduced cost per ton.
- The pump suction inlet is located above water surface. Approximately 1-1/2″ of vacuum is required to lift water and solids one foot above the water surface. Actual measurements on a 10″ dredge show a 15″ vacuum in the suction pipe at water surface and a 24″ vacuum reading at the pump inlet when the pump inlet is 6.5′ above the water surface.
- An adequate supply of pumpable solids is not available at the suction inlet. This condition is indicated when vacuum cannot be readily maintained at the desired level. Use the proper digging device on the suction inlet and operate it correctly. If solids are not available to be pumped, a jet system will not increase production.
- The suction pipe inlet is partially plugged. Use the correct digger device and operate it properly.
- Dredge system pipeline velocity is too fast. Use a velocity meter, experiment and find the target velocity, usually in the range of 12 to 16 fps in the discharge line. Keeping the suction line velocity low (but not too low) reduces friction loss and makes more vacuum available to lift solids to the pump.
- Oversized suction pipe (low velocity). If the suction line is more than one pipe size larger than the discharge pipe size, check the velocity in the suction pipe. If it is too slow, the suction pipe will partially plug with solids and greatly reduce the rate of production.
- Undersized suction pipe (high velocity). If the suction pipe is the same size as the discharge pipe, vacuum may be wasted in overcoming higher friction losses caused by too-high velocity. The suction pipe usually should be one size larger than the discharge pipe.
- Dredge pump is not properly adjusted. A large running gap between the suction sideliner and the impeller: a.) increases recirculating flow inside the pump: b.) soaks up power, c.) increases wear rate and d.) diminishes pump performance.
- Dredge pump is worn out. The pump’s ability to maintain a high vacuum usually decreases as the pump impeller vanes wear away from the eye. It is false economy to try to get every last pound of production out of a dredge pump before replacing parts.
- Suction line air leak. Any air leak decreases the pump’s ability to “pull” a high vacuum.
- Packing gland air leak. If the packing gland is not doing its job properly, the gland will seal as long as the vacuum is low, however, when vacuum increases to 18″ or more, air may enter the pump. The pump will then cavitate and may occasionally lose prime.
- Suction sleeve tube is collapsing under high vacuum. Test for this condition by installing a vacuum gauge tap at the inlet end of the suction hose and comparing its reading with that of another vacuum gauge located near the pump inlet end of the hose. When pumping solids at about 14 fps velocity, the difference in vacuum readings should be not exceed two times the vertical distance in feet from one gauge tap to the other.
- A short, straight suction pipe conserves vacuum.
When the effects of the above factors has been eliminated or minimized and production is still not satisfactory, it is time to consider installing a suction jet assist system or a ladderpump.
The Jet Assist System
Jet assist system components include a power unit, a water pump, the jet body and connecting piping. The power unit and water pump can be located any place on the dredge, preferably at some distance from the operator so to not add noise to his environment.
The jet body consists of a steel or cast housing with flanges on each end for attachment to the suction pipe. The housing contains a replaceable venturi section, a replaceable liner section at the discharge end and provision for one (single jet) or two (twin jet) water nozzles. The position of the nozzle(s) relative to the venturi is very important. Also, the shape of the venturi throat, the size of the nozzles and water pressure are also critical to the performance of an efficient jet assist.
Single jets are designed for installation on plain suction pipes. Ordinarily these pipes are bent downward at an angle to form a âstinger.â The single jet can be substituted for the elbow and the jet suction pipe becomes the âstinger.â Single jets are available with 30 degree and 45 degree inlet ports.
Twin jets are designed to fit into a straight suction pipes such as found on rotary and linear cutter ladders.
Jet manufacturers claim that there is no difference in efficiency between single and twin jets. Jet efficiency is so poor that a variance of 5% or so would probably not be noticed anyhow.
Suction jet assist system wear parts are the water pump guts, the jet nozzle(s) and the venturi and liner sections. Solids and water mix with tremendous turbulence in the jet body, which makes wear unavoidable. Water squirts out of the high pressure nozzles at close to 80 miles per hour and collides with slurry that is only moving about 7 mph. Replace worn parts to maintain peak jet performance and pump only clean water through the jet nozzle(s).
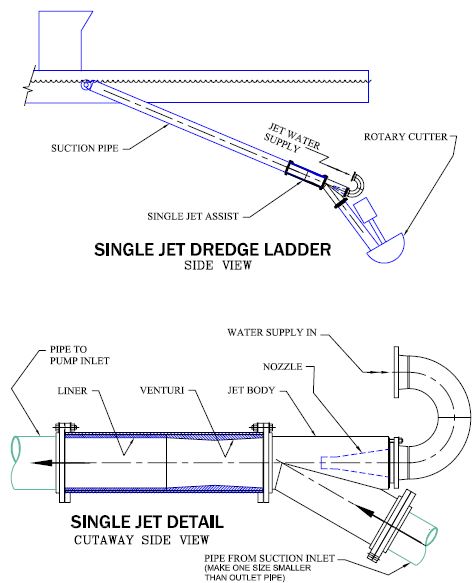
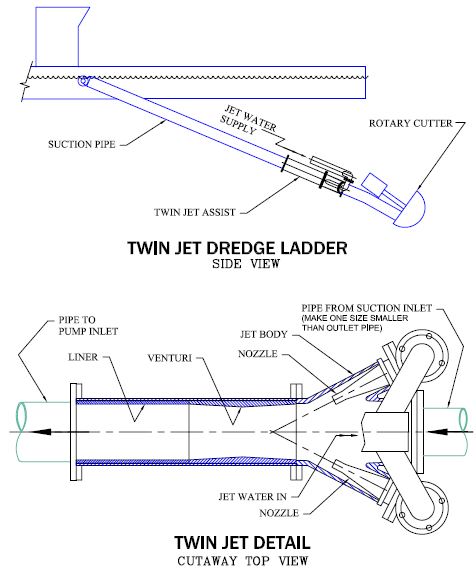
Jet Location
What is so difficult about installing a jet? Just chop a section out of the suction pipe as close as possible to the suction inlet, install the jet, hook up the water supply and away you go.
That is about as technical as jet installation instructions ever get. But, why should it be as close as possible to the suction inlet? I have asked and never have gotten an answer to that question. The lack of an answer probably comes from not knowing. I know why. No, I donât why they donât know, I know what they donât know.
Simply chopping a section out of suction pipe and inserting the jet means that the jet outlet and inlet pipes will be the same size. Let us call these pipes respectively, the pump suction pipe and the jet suction pipe.
Most jets are simply inserted into the suction pipe with no thought that there may be unintended consequences. The function of the jet assist is to inject water into the slurry flow as it rises to the pump inlet. If 33 to 50 percent of the water enters the flow through the jet body, the balance of the flow has to come through the suction inlet. The velocities of the flows are proportional to the flow rates as long as the pipe size remains the same. If the velocity of the flow coming into the pump is 10 feet per second and 40 percent of the flow enters through the jet then 60 percent of the flow has to come in through the suction inlet. Since the pump and jet suction pipes are the same size the velocity in the jet suction pipe will only be 6 fps. Pretty darn slow. Maybe too slow. Might plug even if it is short.
Might plug if it is not short enough.
The reason the unknowing say that a jet has to be located as close to the suction inlet as possible; to prevent jet suction pipe plugging. But it does not have to located near the suction inlet if you have some understanding of what goes on in the suction pipes.
Read on and find out why a smaller jet suction pipe is a good idea and allows flexibility in locating the jet in the suction pipe.
Suction Inlet Velocity
The typical arrangementâsame-size-suction-pipesâdescribed above, causes decreased velocity at the suction inlet, which can result in jet suction pipe plugging.
An oft-asked question at seminars is, âHow far will the suction âpullâ solids?â The answer is usually, âAbout one pipe diameter.â or some other shoot-from-the-hip value delivered in an authoritative manner. No one ever seems to doubt the answer to this question, whatever it is. They always go away happily clutching this little nugget of useless information.
The actual distance does not matter. A dredge is not going to âsuck solidsâ if they are too far away from the suction inlet; somewhere beyond the âpullâ distance. Production demands that conditions at the suction inlet cause sufficient solids to enter. Pumpable solids must be within âpullingâ distance.
What are the conditions?
- Suction pipe velocity
- Size of the suction inlet.
- Shape of the suction inlet.
- Solids particle size distribution.
- Availability of pumpable solids.
One hard fact rules. The velocity must be fast enough to cause pumpable solids to enter the suction inlet. Particles will not move until they are subjected to a flow with a velocity that is fast enough to cause them to move. Velocity must increase as particle size increases. Fine sand will move in a 5-fps flow while coarse rock may not move unless the velocity is 17 fps or more. Particles imbedded in the solids bank are unlikely to move in sufficient quantities unless they have been loosened and turned into pumpable solids by mechanical means. Maximum, continuous production is totally dependent on there being an ample supply of pumpable solids available at the suction inlet. Partial or complete immersion of the suction inlet in pumpable solids creates conditions favorable to maximum production.
Plain suction has no ability to reach out and âgrabâ solids. The solids have to be incorporated into the flow and the only way to assure a constant and ample supply of pumpable solids is to use a mechanical digging device. Spray jets are grossly inefficient.
The idea of immersing the suction inlet in pumpable solids may be foreign to some dredgers. They are more comfortable with the old fashioned way of doing things; partial immersion: keeping the suction inlet only as close to pumpable solids as necessary to maintain vacuum.
Consider a new conceptâimmerse the suction inlet in the pumpable solids and let a CONVAC modulating bypass valve do the work. This system maintains vacuum at the value selected using a touch pad. The operator keeps the suction inlet immersed in pumpable solids and adjusts the vacuum occasionally to maintain target velocity. A lot less work and a lot more production.
Jet Suction Pipe Diameter
I recommend that the jet suction pipe always be one size smaller than the pump suction pipe to maintain adequate velocity at the suction inlet. First hand experience shows that this arrangement works very well. The typical reduction in area between pipe sizes is about 25 percent so a one-size-smaller jet suction pipe will result in an increase in velocity of about 25 percent. The 6 fps jet suction pipe velocity in the example above would increase to a more comfortable 8 fps.
The fact that one manufacturerâs standard jets feature inlets one size smaller than the outlets is further evidence that the one-size-smaller jet suction pipe concept is valid. These folks really understand how their products work.
If the jet suction pipe is one size smaller that the pump suction pipe, the jet can be installed at any convenient place in the lower half (suction inlet end) of the suction pipe without fear of plugging.
Checking Jet Assist Performance
One manufacturer suggests that their jet is performing well when vacuum at the dredge pump inlet is less than 4 inches when pumping clear water at target (solids pumping) velocity. That method does not allow for factors such as pump height above water or ladder length. I have seen jets that create a pressure of 3 to 5 psi positive pressure at the pump inlet.
A better test is to pump clear water at the target velocity and note the vacuum, then shut off the jet water pump and note the vacuum. The difference in the two readings is the effective vacuum being put into the system by the jet system.
When the jet assist system is new or newly overhauled, record the service water pressure and the vacuum at the dredge pump inlet while pumping clear water at a discharge pipeline velocity of 14 fps. Shut off the jet pump and record the vacuum being sure that the velocity is still at 14 fps. Record the diameter of the orifice of the nozzle or nozzles and the diameter of the venturi throat.
Repeat the test occasionally. If the water pressure stays the same and the jet-running vacuum is higher and the jet-pump-off vacuum is lower than the when-new recorded values, venturi wear is indicated. Change the venturi when jet performance is not adequate to sustain production. Be sure to change the venturi before wear occurs on the jet body casting.
If water pressure decreases, it indicates wear in the pump or nozzle assuming that other water uses have remained constant. Check the nozzle bores for wear. If the nozzles are not worn, be sure that water usage has not increased at some other point in the service water system.
If pump performance is suspected, borrow a flow tester from the local fire department and check the water pump performance against its performance curve before tearing it down for rebuilding.
Nozzle wear is indicated when the electric motor powering the water pump starts to overload even though the pressure remains constant. The motor may be overloading because the worn nozzles are allowing too much water to enter the jet. Pumping extra gallons requires extra horsepower.
If the nozzles are too small, the amount of water injected into the suction pipe may be less than 30 percent of the total flow going through the dredge pump. Low flow will reduce the already low jet efficiency.
If pressure falls below 100 psi, jet efficiency will also fall.
Note that the nozzle size and jet pressure must be balanced to accomplish the desired effect–that of increasing production.
Oversized Jet
It is possible to have too much jet assist. If the pressure is too high or the nozzles too large, the result will be a jet flow that is somewhat greater than 50 percentâthe maximum recommendedâ of the dredge system flow. Production will be less that it could be.
The reason is that if the jet contributes too large a proportion of the flow moving up the suction pipe, the velocity at the suction inlet will be so slow that solids will not be picked up. The symptoms of this problem include the inability to increase vacuum at normal velocities and the necessity to pump at higher than target velocity. The jets contribution to flow is essentially fixed by the nozzle diameters and the pressure. The only way inlet velocity can be increased to cause solids to flow into the suction inlet is to increase system velocity.
Case History
A dredge was undergoing an overhaul and as a matter of course, the jet assist body was dismantled to check for wear. It was found that one of the two nozzles was plugged with sand. It had obviously been plugged for some time because the wear pattern on the venturi indicated that only one nozzle had been working. The screen on the water pump inlet had too small an opening to pass a nozzle-plugging rock to enter the system. How could the nozzle have become plugged?
After a review of operating procedures, it was found that the dredge operator, when shutting down the dredge, often slowed the jet pump diesel to idle at the same time that he idled the main pump engine and disengaged the pump. The backwash at one time must have contained enough solids and pressure to fill the jet nozzle and it plugged the next time the jet was run. The nozzle stayed plugged because there was no way for it to reopen by itself.
And the moral of this story? Check your jet occasionally
to be sure both nozzles are open and do not shut off the
jet as long as the dredge system is back-flushing.
In Memoriam Mr. Roy Smalley |
Not long after I came on the dredge scene, I met the âJet Kingâ. Roy sold for Thomas Foundries (Now Svedala) and he had adopted the suction jet assist as his baby. He was utterly convinced and thus able to convince others of the merits of a jet. His enthusiastic presentations conveyed his unswerving conviction that a jet could absolutely solve any dredge problem. He was hard to ignore. I called on a lot of producers who swore by Royâs jets and I also saw several producers who had new jets laying in their yards–jets they had had for years. Roy sold jets. May the Jet King rest in peace. |
Comment, question, criticism, information on products mentioned? Contact willard@willardsays.com