Willard Says……
The Whistlepipe is a simple collection of pipe parts connected to a booster pump inlet pipe. It prevents or diminishes the occurrence of water hammer (pressure spikes) and the consequent damage that may result due to pump cavitation. The sketch at the bottom of the page provides more detail.
Cavitation
Cavitation is a booster pump’s deadly enemy. It occurs whenever liquid does not flow into the pump’s inlet port in quantity sufficient to equal the flow leaving its discharge port. Cavitation occurs whenever the vacuum on the inlet side of a pump exceeds the Net Positive Suction Head Required (NPSHR). In other words a cavitating pump is “starving.” A more complete explanation can be found in Willard Says…Cavitation.
Cavitation can cause:
- Packing gland damage. Cavitation causes the impeller and shaft to vibrate. The movement of the vibrating shaft opens the gap between shaft sleeve and packing.
- Pump shaft breakage. Frequent or continuous impeller/shaft vibration overstresses the shaft. Eventually the shaft breaks.
- Accelerated pump wear. Cavitation causes vacuum-filled bubbles to form near the impeller vanes. When the bubbles collapse they actually peck metal out of the impeller.
- Decreased Production. Cavitation interrupts normal pump function. The pump cannot maintain normal flow in the pipeline system while cavitating.
- Pump case breakage. Pressure spikes come in all sizes. Large ones will break the cleanout cover, the suction side cover or even the pump case.
Water Hammer
Water hammer is a pressure spike that occurs when a moving column of water flowing in a pipe collides with a stationary column of water residing in the same pipe—a situation caused by cavitation.
Water hammer causes the “thunk”
you may hear in your home water piping system when you quickly close
a faucet. As with any
collision, the potential
for damage is largely dependent on the relative
speeds of the colliding columns of water.
The Whistlepipe
The drawing at the bottom of the page details a typical Whistlepipe arrangement. The chart suggests nipple & check valve size and quantity and riser pipe size for various sizes of inlet pipe. Use iron or bronze check valves—no plastic!
Disclaimer: Nothing in this paper should be construed as a warranty. A Whistlepipe is considered to be good insurance and not absolute protection against damage. |
Occasionally, I see a riser pipe topped with one large check valve. Functionally, there is nothing wrong with that arrangement except the cost of a large metal check valve is large compared to the cost for two or three small ones.
A Pump Salesman Story
Allow me to digress and relate a pertinent Pump Salesman story. Ace the Pump Salesman had succeeded in selling a 2-pump dredge of his design. This Rube Goldberg 12-inch dredge directs the output of an 8-inch ladderpump to an 8-inch hullpump. That’s right—eight boosted by eight equals twelve. The inlet of the hullpump (acting as a booster) did not have a Whistlepipe. Shortly after startup the ladderpump hiccuped and the booster pump got an overdose of water hammer which caused the cleanout cover to blow off and nearly take out a deckhand. This incident was hard to ignore and there was little enthusiasm for a repeat performance.
Ace, knowing little about pumping and even less about dredge design, had no clue as to how to prevent a reoccurrence. Searching for an answer, Ace called some other dredge gurus and one enlightened soul suggested a Whistlepipe. This idea was moved, seconded and approved. While the crew installed a riser pipe, Ace the Pump Salesman went to town to get a check valve. Succumbing to either a brain fart or an urge to pinch pennies, he bought a large PVC check valve. Soon another jolt of water hammer launched the shattered plastic check valve into low orbit. Enlightened and miraculously unscathed, they then installed a metal check valve. Problem solved.
Whistlepipe Function
During normal dredge/booster operation the pressure in the booster inlet pipe keeps the Whistlepipe check valves closed (that is not to say that they will not leak). If the flow from the dredge pump slows or stops the pressure in the inlet pipe will decrease to a vacuum, the check valves open and air will be drawn into the booster pump. The bubble of air trapped in the booster pump serves two functions.
- Air entering a centrifugal pump will cause it to lose prime and cease trying to pump liquid. Air disables the pump by forming a bubble in the impeller eye. In this condition the pump could be said to have a harmless case of “indigestion.” A “belly full of air” makes it possible for the booster to continue running without damage in the absence of an adequate supply of slurry.
- The bubble of air in the booster pump case serves as a cushion to prevent or considerably diminish the pressure spike that occurs as the flow from the dredge accelerates to meet the slow-moving or standing slurry in the booster’s discharge pipe.
If air is not allowed to enter through a Whistlepipe the cavitating booster pump will contain a whirling froth of slurry and vacuum-filled vapor bubbles as it tries to pump. As the accelerating pipe full of water from the dredge moves toward the booster pump these bubbles will collapse instantaneously as the pressure increases. The stage is then set for the incompressible incoming column of slurry to collide with the incompressible pipe full of water that is at rest or moving slowly in the booster pump discharge pipe. A pump-busting pressure spike may result.
The air bubble, having acted as a shock absorber and cavitation antidote, is flushed to discharge as normal flow through the dredge system resumes.
Why did the Ace the Pump Salesman’s plastic check valve blow off? Because there will always be a pressure spike whenever the flow from the dredge to the booster pump slows or stops. This situation is exacerbated when the pumps are close together, such as on a double-pump dredge. For that reason metal check valves should be used on the Whistlepipe to contain moderate pressure spikes.
Installation note:
An Ohio booster operator blew up a pump shell twice and then installed a Whistlepipe. He reported that the Whistlepipe was worthless; his pump had blown again. A classic case of knowing the result, but not the reason.
Investigation revealed that he had a discharge sleeve in the line between the Whistlepipe and the booster pump inlet. When the pump started to cavitate vacuum caused the discharge sleeve to collapse and prevent air from entering the pump shell. He had no more problems after making sure that there was vacuum-proof piping between the Whistlepipe and the booster pump inlet.
Conclusion
Having a correctly installed and configured Whistlepipe on a booster pump inlet is cheap insurance. Once installed the Whistlepipe is invisible as regards system operation. If yours is the rare dredge system that never suffers a pressure spike you are fortunate. The Whistlepipe valves will remain closed but standing guard just in case. More likely your system will experience pressure spikes and you will benefit by having a Whistlepipe. Your choice.
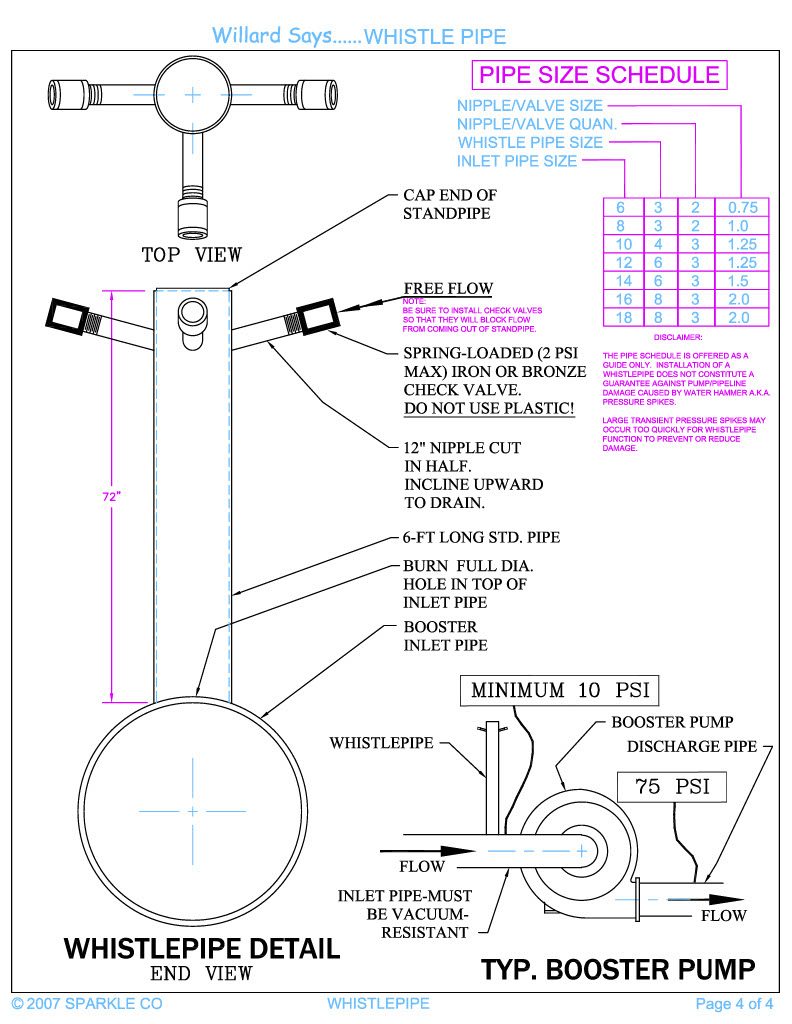
Comment,
question, criticism, information on products mentioned? Contact willard@willardsays.com